ManWinWin is a mixed equipment maintenance management software that makes the maintenance staff work easier. Plus, it helps them track and run a repair on equipment and assets from every sector: hospitals, industrial plants, malls, government facilities, and ports.
If your goal is to reduce costs and equipment downtime, ManWinWin is easy-to-implement, flexible, and easy to use for equipment maintenance and management.
Few of its essential feature: equipment dashboards and datasheets that gives all the information about asset components, codes, location, vendor information, a checklist of tasks that needs to be completed by maintenance staff that provides the record of the maintenance history of all the equipment.
Advantages
- Overall experience is very pleasing
- User-friendly dashboards
- Well-structured
Disadvantages
- You can’t easily skip a step (even if you don’t need it)
- Not a useful tool in the long run
- It’s very difficult to update
Summary
Comments
Brad Haddin
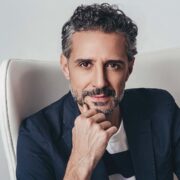
ManWinWin is an easy-to-use and reliable tool for managing equipment maintenance, offering great tracking, scheduling, and reporting features. Limited third-party integrations.
Anton Roux
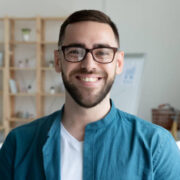
ManWinWin is user-friendly equipment maintenance and management software. It offers great flexibility, detailed asset tracking, and efficient maintenance scheduling—making it an ideal choice for businesses. But there is not many distributor in every country.
Jason Smith
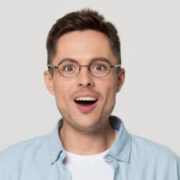
ManWinWin is a user-friendly equipment maintenance software that helps schedule tasks, track assets, and manage inventories. Its intuitive interface and customizable features make it a great choice for improving efficiency and reducing downtime. One con of ManWinWin is that its advanced features may have a steeper learning curve for new users.
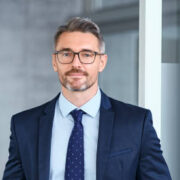
While ManWinWin offers a comprehensive set of features, its user interface can feel a bit dated, and the learning curve may be challenging for new users. Additionally, some users may find the pricing on the higher side for smaller organizations.
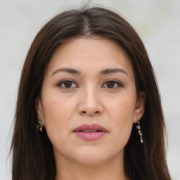
It’s an excellent help for maintenance management. While working on it, we realized that it’s developed by those who have worked on the ground level and understand equipment management from the core.
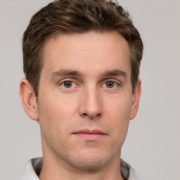
The capability of having all the maintenance management colleagues utilize it simultaneously is incredible. We can feed the data from multiple locations and can all access it simultaneously—a handy feature and software.
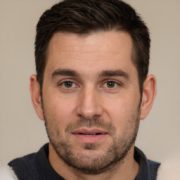
The software is very easy to use. It is a system that can be managed on a factory floor and operated by hundreds of employees without any problem.